Stormwater
Runoff Best Management Practices For Marinas: A Guide for
Operators Jay Tanski, New
York Sea Grant Extension Program, Cornell Cooperative
Extension
Partial
funding for this publication was provided by New York State
Department of Environmental Conservation Section 319 Program and
U.S. Environmental Protection Agency Peconic National stuary
Program.
This
information is provided for educational purposes only. Mention of
trade names, products, companies or services does not imply
approval, endorsement or recommendation by the New York Sea Grant
Program, Cornell Cooperative Extension, N.Y. State Department of
Environmental Conservation or U.S. Environmental Protection
Agency. Although this work has been funded in part by the U.S.
Environmental Protection Agency under Assistance Agreement No.
01-440-498-18-00019 to the Suffolk County Department of Health
Services, it may not necessarily reflect the views of the Agency
and no official endorsement is inferred. Acknowledgements:
The author wishes to thank Peter Needham, Coecles Harbor Marina;
Allan Connell, U.S.D.A. Natural Resources Conservation Service;
Tom McMahon, Suffolk County Soil and Water Conservation District;
Gil Kelley, No-Chem Paint Stripping, Inc.; and Barry Dubin, Dumond
Chemicals for their practical and technical
expertise.
Stormwater
runoff and Best Management Practices, or BMPs, are buzzwords being
used more and more when people are talking about environmental
protection and water quality. They are also terms marina owners and
operators are hearing more frequently in relation to their
facilities. But what do these terms mean and how do they relate to
marina operations from a practical perspective?
This guide
provides a brief discussion of why stormwater runoff management is
important at marinas and the types of things facility owners can do
to address this potential problem. The emphasis is on providing
information that will familiarize readers with the options available
and help them begin to screen these options in terms of potential
application at a specific site. Although intended primarily for
marina owners and operators, this information should also be of
interest and use to others involved with boating facilities and
environmental management including government and agency officials,
planners, consultants and the public.
Stormwater
Runoff, Hull Maintenance and BMPs - They All Go
Together Stormwater runoff is simply the water from rain and
snow melt that flows across the land. This water picks up pollutants
left on the land and carries them into wetlands, creeks and bays
where they can adversely impact water quality and threaten aquatic
habitats. Any development can increase the amount of stormwater
runoff, alter natural drainage patterns, and increase the
concentration and types of pollutants carried by the
runoff.
Even
relatively simple practices can help reduce potential pollution
from hull maintenance areas.
For marinas, runoff can be a concern particularly in areas used
for boat hull maintenance. Due to the materials and compounds used
on boats to control fouling and corrosion and for repairs, the wastes
generated by sanding, scraping, painting, varnishing and fiberglassing
can contain contaminants like metals, solvents and hydrocarbons.
Preparing a
vessel for painting can generate paint chips, dust and particles
that may contain metals such as copper, zinc, and lead. While some
of these metals are relatively harmless on land, if they are not
handled properly and allowed to get into the water, they can be
toxic to marine organisms even at very low levels. (These levels are
so low their harmful concentrations are often measured in terms of
parts per billion). Since many contaminants tend to attach
themselves to solid particles, even soil and dirt in hull
maintenance areas can pick up potentially harmful materials. In
addition to adversely affecting marine life, material washed into
the water from hull maintenance areas can also contaminate sediments
in the marina basin, posing problems for dredging and the disposal
of dredged material. Finally, allowing pollutants to seep into the
ground can eventually contaminate the site itself, posing problems
if the marina is ever to be sold.
So, it is not
hard to see why it is important to keep a close eye on hull
maintenance areas to ensure that the associated wastes do not get
into the water. Under the Federal Coastal Nonpoint Source Pollution
Control Program, the States are required to develop plans to reduce
pollution from stormwater runoff from a variety of sources,
including marinas. While marinas are usually not considered a major
contributor to water quality problems, existing marinas are being
asked to reduce the total amount of solids in runoff from boat
maintenance areas by 80 percent as part of this program. The
question is how best to do this.
This is where
Best Management Practices come in. Put simply, BMPs are really
anything a marina operator can do to help prevent or reduce the
amount of pollutants coming from his facility. BMPs can involve a
wide range of activities including:
- Building
new structures,
- Using new
or different equipment or products,
- Changing
operating procedures and improving housekeeping practices.
Which BMPs are
really "best" for a particular facility depends on the
marina.
Different
Marinas, Different BMPs When evaluating BMPs for use at a
site, it is important to remember all marinas are different and, in
some respects, unique. Marinas in different parts of the country can
vary tremendously in terms of their average size, services offered
and operating characteristics because of differences in boat use,
number and size. Even in relatively small geographic areas there can
be a great deal of variation in the facilities. In the New York/Long
Island metropolitan region, marinas range in size from less than 10
to more than 500 slips. Gross annual revenues range from $14,000 to
$15,000,000 with most of the facilities falling towards the lower
end of the range.
Obviously, the
diversity in size and types of marinas makes it difficult to
generalize about BMPs for these facilities. A BMP that works well at
one marina might be totally inappropriate for another because of
location, site, economic or operational considerations. Each marina
must be examined on a site-specific basis to ensure that the most
effective and suitable BMPs are selected.
While there is
no "one size fits all" set of BMPs for all marinas, there are a
number of BMPs often suggested for reducing potential stormwater
pollution from hull maintenance areas. Chances are one or more of
the BMPs discussed here would be suitable for most facilities.
BMPs are often
categorized into two types commonly known as Source-control BMPs and
Stormwater-treatment BMPs. Source-control BMPs focus on keeping
stormwater from coming into contact with pollutants.
Stormwater-treatment BMPs usually involve building structures or
installing devices to treat or manage runoff. Source-control BMPs
are generally preferred because they usually cost less and can keep
most, if not all, of the pollutants out of the water.
MAINTENANCE
AREA SOURCE-CONTROL BMPs Indoor Maintenance Areas
Moving maintenance and repair work indoors or under roofs
where it is not exposed to rainfall is one of the most effective
ways to reduce contaminated stormwater runoff. However, it may also
be one of the most impractical alternatives for many marinas due to
cost, size and space limitations, and zoning restrictions,
especially when traditional structures are used.
For marinas
with enough room, temporary work enclosures, such as the one shown
here, can be a relatively inexpensive way to protect maintenance
areas from rain while extending the work season. The enclosures are
pre-fabricated structures made of heavy-gauge polypropylene plastic
stretched over a tubular metal frame. Although the plastic has a
life expectancy of three years, this structure is seven years old
and has survived a hurricane and a number of severe "northeaster"
storms without major damage.
Planning
Considerations Indoor work areas should have hard floors to
facilitate clean up. Floor drains should be avoided or covered while
work is being done.
Temporary
enclosures come in various sizes up to 100 feet long, 30 feet wide
and 23 feet high. Usually, enclosures come as a kit with
materials and assembly instructions. The marina must supply the
labor to actually build the structure. Construction does not usually
require special tools or skills, but it can be time consuming.
Because they
do not have permanent foundations and are considered temporary or
portable, these structures may not require permits or zoning
approvals in some locations and may also be exempt from capital
improvement taxes. Check with your local building department
regarding the laws and regulations in your area.
Moving certain
types of work, like painting, indoors or into enclosed areas may
require the use of special ventilation equipment, protective
clothing and respirators, and safety equipment to meet Occupational
Safety and Health Administration, Clean Air Act, and local fire
safety requirements and regulations.
Cost Buildings
capable of handling boats can cost over $60 per square foot to
construct in the New York area, not including land costs. (All cost
estimates in this document are given in 1997 dollars unless
otherwise noted.) Unless a building is already available, it is not
feasible for most marinas to build a structure solely for
maintenance activities. Typical costs for temporary work enclosures
run between $3 to $5 per square foot for materials. This does not
include labor.
Outdoor
Maintenance Areas Usually, it is not practical for marinas
to do all maintenance work under a roof. If work has to be done
outdoors, it should be done over dry land in specially designated
areas designed for that purpose. These areas should be clearly
marked with signs. Customers (and staff) should be discouraged from
performing maintenance work outside these areas.
Planning
Considerations Locate maintenance areas as far away from the
basin as possible to prevent contaminants from getting into the
water.
Maintenance
areas should have a hard, impermeable surface that can be easily
vacuumed or swept to remove contaminants. Concrete surfaces are
particularly easy to clean and resistant to solvents and petroleum
products.
Maintenance
areas should be swept or vacuumed regularly and the collected wastes
disposed of properly. Special attention should be paid to weather
conditions, with cleanups being done more frequently if there is a
chance of material being dispersed by wind or rain. Avoid hosing
down the work area.
Care should be
taken to ensure that stormwater runoff from other parts of the
marina does not flow over the maintenance area. This can be done by
proper siting or by using berms, curbs, or one or more of the
stormwater treatment BMPs discussed below to divert water from the
area.
If the
maintenance area cannot be properly cleaned, rainwater falling on it
should be directed to a stormwater treatment device before being
allowed to run into the marina basin.
Maintenance
areas should be located away from storm drains. If storm drains are
nearby, they should be covered when work is being done to prevent
material from being carried into the marina water. If blasting or
painting is done outdoors, vertically hung tarps or enclosures
should be used to contain dust, abrasive grit and/or paint. Work
should be monitored, especially on windy days, to ensure paint, dust
or blasting grit is contained and stopped if conditions prevent
containment.
Cost Costs
for hull maintenance areas vary widely depending on the specific
marina. In some cases, existing infrastructure, such as parking lots
or other paved surfaces may be converted to maintenance areas with
minimal expenditures. Curbs or berms may be installed for
approximately $10 to $12 per foot. Constructing a new concrete pad
with appropriate runoff controls capable of handling large boats can
cost $20,000 or more in the New York metropolitan area.
Work
Outside of Designated Hull Maintenance Areas In some marinas,
it may not be possible to have a designated work area for all hull
maintenance activities due to space limitations, time constraints,
or cost. If work has to be done outside a designated area,
precautions should be taken to contain wastes and debris and prevent
them from entering the water. Tarps used to contain paint chips
and dust from hull maintenance activities.
Planning
Considerations In areas that do not have sealed or impervious
surfaces, perform all work over tarps or drop clothes. Ideally,
tarps should be placed beneath the cradle or boat stand.
If customers
are allowed to do maintenance work on their boats, they should be
required to clean up the area when done working. Separate, covered,
and labeled containers should be provided for waste
materials.
When
maintenance work has to be done near water, consider the use of
additional BMPs such as the innovative paint removal techniques and
dustless vacuum sanders described below.
Innovative
Paint Removal Techniques Different paint removal technologies
can be used as BMPs to eliminate or, at least, contain paint chips
and dust associated with hull preparation activities. Special
equipment, products or procedures can also help reduce the amount of
waste material generated and ensure it does not get into the
environment.
Plastic
Media Blasting: New abrasive hull blasting technologies utilize
a process to reclaim and reuse media made of plastic. In this
procedure, the boat must be completely enclosed to trap the media
and paint waste. The collected mixture is fed into specialized
equipment (located in the truck in the photograph) which through a
sifting process separates most of the paint dust and chips from the
media, which can then be reused. In addition to containing paint
dust and chips, this process can significantly reduce the amount of
material that has to be disposed of when stripping a hull. For
example, the plastic media stripping of a 19-foot boat produced a
total of 200 pounds of waste and media. The equipment recovered 185
pounds reusable media (containing a small amount of paint), leaving
only 15 pounds of paint for disposal.
Planning
Considerations Specialized equipment and training is required
for plastic media blasting. In some areas companies have mobile
equipment and will perform this service on site for a set
fee.
Containment of
dust and other debris and recovery of the media can considerably
reduce clean up and disposal costs.
Since the
media can not remove anything harder than itself, these techniques
may not be effective for preparing all surfaces. For instance,
plastic media may not remove corrosion or barnacles from props,
shafts, or rudders. However, it will remove paint without damaging
sound gel coat, rubber, chrome or glass surfaces.
Some softer
media may not work well on very durable, pliable paints (like coal
tar epoxies). Paint around edges may have to be removed by hand.
Sanding is usually required before painting a blasted
hull.
Care should be
taken when blasting boats that have damaged or blistered gel coats
since blasting may open blisters or voids that have to be filled
before painting. Even sound gel coat may contain small voids that
may have to be filled after blasting.
Cost Equipment
costs for a blasting system that incorporates media recovery and
reclamation start at $25,000, not including training or the media.
In New York, contractors with their own mobile equipment will blast
hulls with plastic media on site for approximately $17 to $18 per
foot, where length is calculated as the length of the boat at the
waterline plus one-half the beam. (Approximate cost for blasting a
"typical" 30-foot power boat is about $630.) Discounts may be
available for volume work.
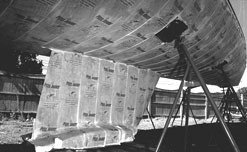 |
Chemical paint stripper and covering cloth
applied to boat
hull | |
"Environmentally-Sensitive"
Chemical Paint Strippers Chemical paint strippers can
actually eliminate paint chips and dust associated with sanding,
scraping and blasting. There are now less toxic and less hazardous
alternatives to strippers that use methylene chloride and other
organic solvents. New products are non-chlorinated, biodegradable,
have low volatility and are not listed as hazardous. Some of the
more environmentally-sensitive strippers may be water based and use
less toxic materials (look for dibastic esters, semi-aqueous
terpene-based products, detergents and C9 to C12-based hydrocarbon
strippers). While the new strippers themselves may be considered
non-hazardous, metals and chemicals from the paint they remove may
be hazardous, so all residue and wash water must be collected and
disposed of properly.
Planning
Considerations Environmentally-sensitive paint strippers are
usually made without toxic or caustic chemicals, so they do not burn
skin and will not release harmful fumes like some of the more
aggressive chemical strippers. This can reduce or eliminate the need
for special ventilation equipment.
The more
environmentally-friendly strippers may require more experience and
expertise to apply correctly, as well as more time to work
effectively. Some may have to remain on the hull for 2 to 24 hours
depending on the condition of the hull and air temperature. Lower
temperatures require longer times, and some products do not work
well below 32°F.
When
stripping, place plastic around and under the work area to catch any
drips. Some products come with a special paper placed over the
stripper after it has been applied that helps contain the chemicals
and dissolved paint.
Strippers may
not work on all paints, such as 2-part epoxies or chlorinated
rubbers. Check with the manufacturer for specific
applications.
Machine used
to pressure wash and collect washwater in one step from chemically
stripped hull. Stripping residue and washdown water may be
contaminated by paint and must be collected and disposed of
properly, possibly as a hazardous waste. Special machines that
pressure wash the hull and collect the washwater in a one-step
process are available for this purpose. It is estimated that a
30-foot boat would generate approximately 30 gallons of waste,
including washdown water.
Cost Costs
will vary depending on product used, conditions, and layers of paint
to be removed. Non-toxic, water-based strippers can cost $40 to $60
per gallon. According to one manufacturer, a gallon of their product
will cover an average of 50 square feet of hull so the estimated
cost of materials is one dollar per square foot. A 30-foot boat may
require five to six gallons. The manufacturer also estimated
disposal cost for the residue to be about $30 per boat depending on
size. Complete pressure washing/vacuum collection systems cost
$5,000 but costs can be reduced if the marina has an existing
pressure washer and/or vacuum system.
Dustless
Vacuum Sanders: Dustless vacuum sanders are sanders (or
grinders) attached to a vacuum system that starts automatically when
the sander is turned on. These units can trap up to 98 percent of
the dust generated by hull sanding, making them particularly
suitable for situations where work must be done near the
water.
Planning
Considerations By containing dust, vacuum sanders keep work
areas and workers clean, saving time and money in clean
up.
To recover
costs, some marinas rent the sanders to customers for use on their
own boats for fees ranging up to $15 per hour. Advertising and
training is necessary to encourage use.
Studies
indicate that sanders may collect an average of two ounces of dust
per foot of boat sanded (3.75 pounds for a 30-foot boat). This
material must be collected and disposed of properly.
Cost The cost
of vacuum sanders varies depending on size and features. Typical
costs range between $1,100 and $1,400.
STORMWATER
TREATMENT BMPs Stormwater treatment BMPs are structural
devices used to manage and treat runoff contaminated with
pollutants. In some cases, these BMPs can also be used to divert
runoff away from areas where pollutants may occur. These devices
normally work by capturing runoff and allowing it to filter into the
ground (infiltration), holding the runoff long enough for pollutants
to settle out (detention/retention) or some combination of these two
processes.
When
considering treatment BMPs, a good understanding of the site in
terms of the drainage patterns and the rate, direction and volume of
water coming from different areas is key to designing an effective
system. In many cases, the services of a professional engineer may
be required to provide this analysis. The information provided here
is intended to help operators and owners evaluate and begin to
screen alternatives for potential applicability at their sites. It
should not be considered a design manual or a substitute for
professional engineering guidance. See "For More Information" for a
listing of more technical publications on this topic.
In general,
marinas should try to reduce the total amount of runoff coming from
the entire facility by using permeable material like gravel or shell
whenever possible outside of maintenance areas. Permeable coverings
slow runoff and allow water to filter into the ground rather than
run directly into the basin. Redirecting slopes away from the
shoreline can also help.
In many
marinas, much of the runoff comes from offsite so it may not be
practical to capture and treat all of the runoff. However,
structural BMPs should be sized to collect and treat at least the
first 0.5 to 1.0 inches of rainfall from impervious work areas. This
is often called the "first-flush" because it usually contains most
of the pollutants. To prevent premature failure, BMPs should also
incorporate provisions for handling overflow from rainfalls greater
than the design rainfall.
There are a
large number of stormwater treatment BMPs, however, not all of them
are applicable to marinas because of space, cost and site
conditions. High groundwater tables, limited space, and aesthetic
and safety concerns are just a few of the factors commonly found at
existing marinas that may limit the type of BMPs that can be
employed. The BMPs discussed here do not cover the full range of
practices available, but they do represent those BMPs that are
generally considered most suitable for conditions commonly
encountered in marinas and for retrofitting existing boating
facilities.
Vegetated
Filter Strip What It Is Vegetation planted as a
buffer along the water’s edge to filter stormwater runoff and remove
contaminants and soil particles before they reach surface waters.
Filter strips can be particularly effective at removing pollutants
that are in the form of large particles, such as paint
chips.
How It
Works Runoff carrying sediments, chemicals and nutrients is
slowed by the vegetation, which allows particles carrying pollutants
to settle out before reaching the surface water. Some rainwater may
filter into the vegetation strip before it can run into the marina
basin. In some cases, nutrients or chemicals in the runoff may be
taken up by the vegetation, rather than going into the surface
water.
Potential
Benefits
- Helps
prevent pollutants from entering waterways, protecting water
quality and keeping sediments in the marina basin free from
contaminants that may impact future dredging operations.
- Can help
reduce sediment deposition in the marina basin, reducing the need
for dredging.
- Creatively
landscaped strips can provide aesthetic and recreational
amenities, such as a picnic area, at a marina if allowed
activities do not disturb the vegetation.
Planning
and Technical Considerations Filter strips must be a minimum
of 20 feet wide to be effective. Wider strips are better in terms of
filtering sediment and pollutants.
Filter strips
are most effective on slopes of 5 percent or less and will not
function well on slopes greater than 15 percent. Steeper slopes
require wider strips. As a rule of thumb, an additional 4 feet of
width should be added for each additional one percent of
slope.
Filter strips
can only handle runoff from relatively small areas (1 to 5 acres).
Care must be taken to ensure that all of the water from the upland
area passes through the strip and cannot bypass it. Since water
has to flow evenly over the strip for it to be effective, the
landward edge of the strip must be at a constant elevation (no dips,
depressions or gullies). A shallow stone trench can be used to
spread the flow evenly at the edge of the strip.
Plants
suitable for the particular area and climate must be used. In marine
areas, salt-tolerant species such as salt meadow cordgrass (Spartina
patens) or "salty alkaligrass" (Puccinellia distans) should be
considered. Your local U.S.D.A. Natural Resources Conservation
Service office can provide information on the best species for your
location.
Strips require
regular maintenance. Reseeding, watering, fertilization and some
mowing may be required to maintain the necessary dense growth of
vegetation. Annual inspections should be conducted and rills,
gullies and channels repaired as soon as possible.
Costs Filter
strips are one of the least expensive stormwater runoff control
measures you can implement. Seeding costs can range from $20 to $100
per 1,000 square feet with sod costing $125 per 1,000 square feet
($0.40 to $6.25 per linear foot for a 20- to 50-foot wide strip)
depending on site conditions.
Infiltration
Trench
What It Is A shallow trench, usually 3 to 8 feet
deep, filled with stone to create an underground reservoir that
holds runoff, allowing it to slowly percolate through the bottom
into the surrounding soil.
How It
Works Runoff carrying pollutants is diverted to the trench
before it reaches surface waters. The trench retains all or some of
the runoff, depending on the design. The stormwater slowly filters
through the soil below, where pollutants are removed by adsorption,
straining, and decomposition by bacteria in the soil.
Potential
Benefits
- Helps
prevent pollutants from entering waterways, protecting water
quality and keeping sediments in the marina basin free from
contaminants that may impact future dredging operations.
- Properly
designed and maintained, trenches can provide effective treatment
for dissolved pollutants as well as particulate matter.
- Relatively
easy to fit into margins and around perimeters of developed areas
with limited space like marinas.
Planning
and Technical Considerations Trenches are only feasible where
soils are well-drained (sandy). The bottom of the trench should be
at least 3 feet above the seasonal high groundwater table and 4 feet
above bedrock or other impervious surfaces (clay).
This approach
should only be used when the contributing drainage area is less than
5 acres and/or the slopes are less than 5 percent.
Trenches can
be designed to collect all or some of the expected stormwater
runoff. "Water quality" trenches that are designed to catch only the
"first flush" of stormwater, which contains most of the pollutants,
may be the only trenches suitable for many marinas because of space
considerations. (To get a rough estimate of first flush volumes,
multiply the square footage of the drainage area by 0.3
gallons/square foot. About 40 percent of the total volume of the
trench will be available to hold water.) Because they are
susceptible to clogging, infiltration trenches should only be used
in conjunction with vegetated filter strips or some other method for
trapping coarse sediments before it reaches the trench. Clean,
washed 1.5- to 2.5-inch stone should be used to fill the trench to
prevent clogging. Blue stone aggregate should be avoided. A layer of
filter fabric placed 6 to 12 inches below the surface can help trap
sediment before it clogs the entire trench, reducing maintenance
costs.
Shallow, wide
trenches (as opposed to narrow, deep trenches) enhance pollutant
removal, but care should be taken to ensure that the stone fill
extends below the frost-line so the trench functions in cold
weather.
Trenches
should be sited away from building foundations. If the trench is
down slope, it should be a minimum of 10 feet from the building, and
100 feet away if the trench is up slope.
Trenches
should be designed to hold water for at least 6 hours after a rain
and to drain completely within 3 days after a storm. A perforated
PVC pipe should be installed as a monitoring well.
Costs: Infiltration
trenches are one of the most economical stormwater BMPs for small
sites. Costs vary depending on the site and the specific design.
Estimates from the Washington D.C. area for a 150-long trench, 6
feet wide and 6 feet deep ranged between $56 and $122 per linear
foot of trench and averaged $83 per foot.
Dry
Well
What It
Is An excavated pit filled with clean stone typically 3 to 12
feet deep that is usually designed to collect and store stormwater
from rooftops or other relatively "clean" runoff.
How It
Works Runoff enters the dry well through an inflow pipe (such
as a roof gutter downspout) and from surface infiltration. The water
then infiltrates down through the subsoil rather than running over
land.
Potential
Benefits Dry wells can be used to manage peak discharges from
storms and reduce the overall volume of stormwater runoff from a
marina site. This, in turn, may help eliminate the need for other
stormwater management measures or reduce the size needed.
Because they
normally collect relatively clean water, they can provide good
quality groundwater recharge.
Planning
and Technical Considerations Because dry wells have limited
pollutant removal capabilities, they may not be effective in areas
with high pollutant loadings unless the runoff is pretreated before
entering the well.
Dry wells are
only suitable for sites where soils are well drained (sandy) and the
well can be designed so the bottom is a minimum of 3 feet above the
seasonal high groundwater table, bedrock or other impervious surface
(clay).
The total
contributing surface area for a dry well system should not be more
than one acre.
Wells are
susceptible to clogging and possible failure from sediment. They
should not be used where they will receive runoff that carries high
sediment loads.
To prevent
clogging and promote infiltration, the well should be filled with 1
to 3 inch diameter clean (washed) stone and lined with filter
fabric.
Locate wells a
minimum of 10 feet away from building foundations.
Dry wells
should be designed to capture, at minimum, roof runoff from a
two-inch rainfall (roughly equivalent to a two year storm on Long
Island). Two inches of rain would generate approximately 1,250
gallons of water per 1,000 square feet of impervious roof (1.25
gallons per square foot). As a first estimate of the size of the
well needed for a particular application, assume about 40 percent of
the total volume of the well will be available to hold
water.
An observation
well should be installed in each dry well to make sure it is
draining properly. A perforated PVC pipe installed vertically in the
well can be used for this purpose. The pipe should have a removable
cap on top and be anchored with rebar at the bottom.
Costs Costs
for dry wells vary depending on the site and design specifications.
Because of similarities in construction, costs for dry wells should
be close to, or perhaps slightly higher, than those for infiltration
trenches which can range between $56 and $122 per linear foot for a
6-foot wide, 6-foot deep trench.
Vegetated
Swale
What
It Is A vegetated channel that looks similar to but is wider
than a ditch, with a gentle slope designed to transport and treat
stormwater runoff. Vegetated swales are also sometimes called
"biofilter" swales and are commonly used as a substitute for curb
and gutter systems.
How It
Works Surface water is directed to a vegetated channel where
gentle slopes and dense vegetation slow water flow. The reduced flow
in combination with the vegetation provide moderate to high removal
rates of particulate pollutants from runoff by trapping, filtering
and infiltration into the soil.
Potential
Benefits
- Can help
protect water quality by removing more pollutants from runoff than
gutters, pipes and ditches or other conveyances.
- Can be used
to divert runoff from areas that may be contaminated with
pollutants, like hull maintenance areas.
- Generally
less expensive than curb and gutter or other drainage systems they
replace.
- Can enhance
the natural landscape and provide aesthetic amenities.
Planning
and Technical Considerations Swales are most suitable for
relatively small sites (less than 10 acres) with low to moderate
density development where the percentage of impervious cover is
small and in parking lots where they can be used to break up the
impervious cover.
Because they
have limited capacity to accept runoff from large storms, other BMPs
may have to be used in conjunction with swales depending on site
conditions and the level of runoff treatment required. The slope
of the swale along its axis should be as close to zero as possible
while still allowing drainage and should never exceed 4 percent.
Side slopes should be no greater than 3:1 (horizontal to vertical).
The site should have well drained soil. Because soil compaction
can inhibit performance, swales should not be used for boat storage
or parking. The bottom of the swale should be at least 2 feet above
the seasonal high groundwater level.
Swales slopes
should be designed to prevent erosion during a two-year storm and
sized to handle the flow from a Ten-year storm. A stabilized outlet
should be provided at the down slope end to prevent scour and
erosion.
Check dams
(railroad ties sunk halfway into the swale with a weep hole and
stone on the downstream side) can be used to flatten slopes and
promote infiltration.
A dense cover
of vegetation must be established and maintained. (Contact your
local U.S.D.A. Natural Resources Conservation Service office for the
best species for your location.) Vegetation should be kept at a
height of at least 4 to 6 inches to promote infiltration.
Maintenance is
minimal and primarily involves periodic mowing, spot reseeding,
debris removal and watering, if necessary.
Costs Swales
are relatively inexpensive. Costs for a 15-foot wide swale with 3:1
side slopes are estimated to be approximately $7.00 to $13.00 per
linear foot depending on the method of seeding.
Deep Sump
Catch Basin and Water Quality Inlet What It Is
Deep sump catch basins (also called oil and grease or hooded
catch basins) and water quality inlets (known as oil/grit
separators) are underground retention systems designed to remove
trash, debris and a portion of the sediment and oil and grease from
stormwater runoff.
How It
Works Runoff is directed or channeled into the top of an
underground chamber or series of chambers that contain a permanent
pool of water. The discharge is located below the inlet pipe. Oil
and grease float on the surface of the water and eventually attach
to the sediment trapped in the chamber, which settles to the
bottom.
Potential
Benefits
- Can help
improve water quality by reducing the amount of trash, sediment
and petroleum hydrocarbons reaching marina waters.
- Underground
installation minimizes space requirements. Usually suitable for
retrofits where larger BMPs are not feasible.
- Can provide
pretreatment for other BMPs such as swales or infiltration
trenches.
Planning
and Technical Considerations Inlets and sump catch basins are
should only be used when the drainage area is less than one acre of
impervious cover.
Because they
provide limited pollutant removal, these devices are often only
recommended as pretreatment devices for other runoff treatment
practices.
For
catch basins, the discharge pipe should be located at least four
feet below the inlet pipe and the depth of the permanent water pool
should be four times the diameter of the inlet pipe. In water
quality inlet chambers, the permanent pool of water should have a
minimum volume 400 cubic feet of water per acre of impervious
drainage area and a minimum depth of four feet.
Oil-absorbent
pads or material can be installed in the basin to further enhance
hydrocarbon removal. In areas with high sediment loads, inlets
and basins should be inspected and cleaned after every storm. At
minimum, they should be inspected monthly and cleaned four times per
year.
Accumulated
sediment and hydrocarbons may be considered a hazardous waste in
some areas. Check with local officials regarding applicable
guidelines and regulations for proper disposal.
Costs Compared
to other BMPs, catch basins and inlets are considered moderately
expensive. Individual catch basins can cost $1,000 to $1,500 to
install. Water quality inlets can cost $5,000 to $15,000 or more.
Maintenance costs can also be high due to the need for periodic
cleaning.
Retention/Infiltration
Chamber What It Is High-density polyethylene
chambers designed to store runoff underground. The chambers have an
open bottom and permeable sides to promote infiltration of the
runoff into the surrounding soil. The units can be linked together
to increase capacity and are designed to be used in place of stone,
pipe, surface ponds and dry wells.
How It
Works Runoff is directed to a catch basin or other suitable
inlet connected to a chamber or system of chambers buried
underground that retain some or all of the water, depending on the
design. The open bottom and permeable sides allow the water to
slowly filter through the soil where pollutants are removed by
adsorption, straining or decomposition by bacteria in the
soil.
Potential
Benefits Helps prevent pollutants from entering waterways,
protecting water quality and keeping sediments in marina basin free
from contaminants that may impact future dredging
operations.
Used as
infiltration devices, chambers provide effective treatment for
dissolved as well as particulate pollutants.
Can be
installed under parking lots and work areas, freeing up surface
space in marinas.
The low
profile (12 to 30 inches) of the units makes them particularly
suitable for use in areas like marinas with high water
tables.
Planning
and Technical Considerations In general, the chamber systems
function in much the same way as the previously-described
infiltration trenches and the same guidelines for site conditions,
sizing, and siting apply.
The individual
chambers come in various sizes but are generally 6 to 7 feet long, 3
to 4.3 feet wide and 1.3 to 2.5 feet high and have capacities
between 75 and 416 gallons. Units are lightweight (22 to 78 pounds)
and can be installed by one to two men without the need for cranes
or heavy equipment.
Depending on
size and design, systems may only require the excavation of a 3-foot
wide, 3-foot deep ditch.
With 18 inches
of properly compacted backfill cover, the chambers are designed to
withstand loads up to 32,000 pounds per axle, making them suitable
for use in areas used for heavy equipment traffic and boat
storage.
A minimum of 3
inches of 0.75- to 1.5-inch diameter crushed, washed stone should be
placed under and along the sides of the chambers.
Inlets should
be equipped with a catch basin, sediment trap or similar device to
intercept sediment and debris to minimize maintenance.
Installations
should be inspected once a year for sediment buildup. Sediment can
be removed by re-suspending with water and pumping the chamber using
access ports built into the units.
Costs Costs
for individual chambers vary depending on size. A 122-gallon unit
costs about $50 to $60 dollars. Manual installation of the units can
also provide cost savings. In New York, system of chambers designed
to handle 1,144 cubic feet of runoff was installed for $1,400 (not
including a site analysis or design costs, or the catch basin) which
is approximately one-third of the cost for a system of similar
capacity using traditional infiltration devices. One manufacturer
estimates an installed system costs between $3 and $3.25 per cubic
foot of runoff capacity.
FOR MORE
INFORMATION The information presented here was derived from a
large number of different sources. Readers seeking more detailed
information on BMP siting planning, selection and design should
refer to the publications listed below. Your regional state
environmental protection agency, Natural Resources Conservation
Service, County Soil and Water Conservation District, or Sea Grant
office can also provide additional information and assistance on
storm water BMP planning and design.
Controlling
Urban Runoff: A Practical Manual for Planning and Designing Urban
BMPs (1987) by Thomas R. Schueler, available from the Metropolitan
Washington Council of Governments, 777 North Capital Street N.E.,
Suite 300, Washington D.C. 20002-4201. Phone: (202)
962-3256
Reducing the
Impacts of Stormwater Runoff From New Development (1992) by
William B. Morton available from the Empire State Chapter of the
Soil and Water Conservation Service, P.O. Box 1686, Syracuse, NY,
13201-1686.
Storm Water
Management. Volume 2: Stormwater Technical Handbook (1997) by
Massachusetts Department of Environmental Protection and Office of
Coastal Zone Management available from the Massachusetts
Department of Environmental Protection, 1 Winter Street, Boston,
MA, 02108. Phone: (617) 292-5500. |